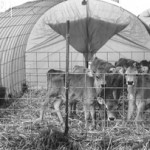
Mechanicsville, Iowa— With more than 400 cows to milk and not a lot of labor on hand, Lee Kurtenbach likes things simple, efficient, effective and cheap. That’s why he’s using wire stock panels covered with tarps to house some 90 separate groups of young dairy calves, five to a group.
Lee calves seasonally starting in early March, and keeps his Jersey bulls until they’re actually worth some money. He needs some shelter in his southern Iowa climate and likes portable calf housing, but in Lee’s view fiberglass domes and the like are too expensive and too much work.
Portable panel/tarp structures have worked well here for several years. Each requires a pair of 16-foot cattle panels (no need for the combination cattle/hog versions), one 16-foot hog panel, a 16-by-12-foot plastic tarp, two steel posts, about 20 plastic zip ties, and a little wire and bale twine.
First he lays the 16-foot cattle panels next to each other, and fastens them together with zip ties. Then the tarp is attached, with one side matched evenly with one of the long sides of the panel structure. He makes sure the tarp is truly 16-by-12, and Lee says it helps to have grommets every two feet, rather than every three-feet as is the case with many cheaper versions.
The hog panel is cut in two, with one piece a section longer (surplus wire is removed). The longer section will be placed in front of the hut, and the shorter one goes in back to reduce the open space that will remain on the back (north) wall once the tarp is tied together.
The cattle panels are bent and tied in with the ends of the hog panels, with the interior ceiling reaching nearly six feet at the middle. A length of twine is tied across the bottom to connect the two ends of the panel structure. Lee says this is very important when the time comes to move these structures, as cutting the twine lets the panels loosen enough to allow easy removal from the bedding pack that was built during the calves’ occupancy.
The loose portion of the tarp is tied together at the back, leaving a gap about eight inches wide and two-feet tall. For early calves, Lee sticks a piece of cardboard into the gap, figuring that by the time the cardboard has been chewed off, the weather will have warmed enough to open the hut a bit anyway. The back piece of tarp is removed once spring warmth sets in for good.
Lee staked the structures down with re-bar until a few of them started rolling across the countryside in big winds. That problem was solved when he switched to pounding steel posts in at the middle of each hog panel section. He drills a hole through each post, and employs a length of wire to connect them to the peak of the roof. No other staking is required.
“We haven’t lost a hut since we started using the posts,” Lee says. They also provide rigidity for attaching a five-nipple feeder. Feed and water containers are attached to a cattle panel side.
These structures allow feeding, watering and bedding without having to enter the calf area. Lee beds heavily when the calves are placed in each structure, but adds very little until they start on grain. When bedding becomes an every-other-day event, Lee knows it’s time to vacate the premises. Each pen is used just once each year.
With wire panel prices seeing a sharp increase in recent months, Lee now figures material costs at around $75 per structure without any volume discounts. He doesn’t re-use the tarps, but figures most people with fewer calves could certainly do so.
For that price, Lee feels his calves are getting an environment superior to what they used to have in fiberglass hutches. And he likes the fact that the panel/tarp structures require a lot less work for the people in charge of calf care.